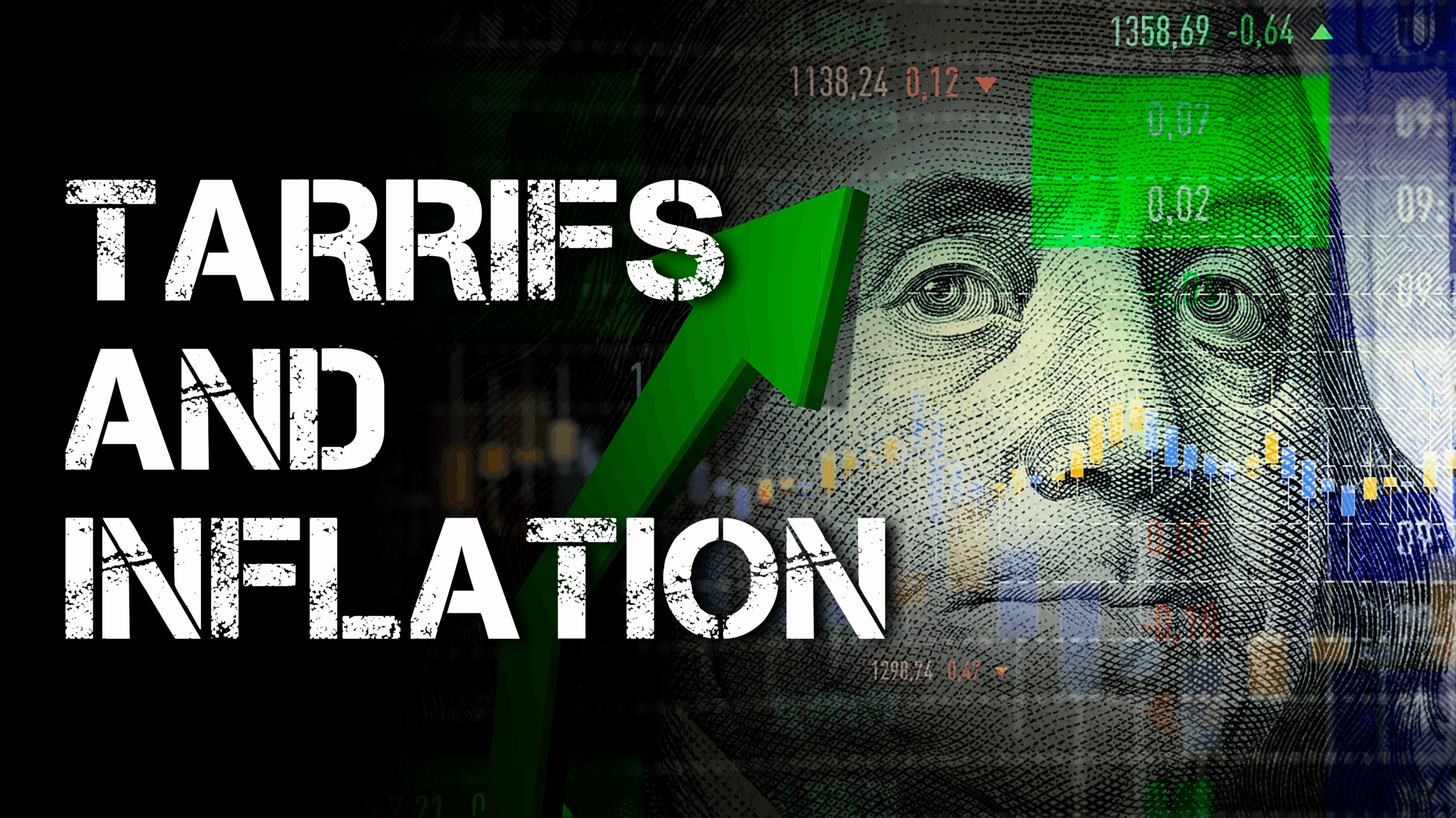
How Tariffs Affect Inflation and Warehousing Space Costs
23 April, 2025
Share to
Tariffs as an Underlying Driver Amid Inflationary Pressure
Inflation is no longer just a macroeconomic concern—it’s a boardroom imperative. Across industries, rising operational costs are squeezing margins, prompting shifts in pricing strategies, and disrupting supply chains. While headlines often focus on consumer demand and monetary policy, tariffs tend to get overlooked as a crucial driver.
Inflation is still a big worry for U.S. businesses in 2025. The Consumer Price Index shows a 2.4% increase from last year as of March, according to the U.S. Bureau of Labor Statistics. This figure may seem moderate, but ongoing cost pressures are hurting margins in many industries. Rising tariffs make this problem worse.
Tariff policies, especially those from the Trump administration and later years, have greatly impacted global supply chains. Designed as trade tools, these levies have become embedded costs that ripple through sourcing, logistics, and distribution, significantly affecting the movement of goods. Today, the legacy of tariff hikes intersects with inflationary pressure to create a perfect storm of cost escalation.
For business leaders in this changing environment, knowing how tariffs affect inflation is important. This knowledge helps them stay competitive and profitable.
How Tariffs Increase Business Costs and Consumer Prices
As CNBC reported in March 2025, Federal Reserve Chair Jerome Powell and leading economists were unequivocal: “Tariffs are simply inflationary.” The report shows how tariffs raise consumer prices. They do this by increasing the cost of goods. This is particularly impacting small businesses that rely heavily on international sourcing.
Tariffs function as indirect taxes. When a 25% import tariff is added to industrial machinery from China, it raises costs. This extra cost impacts importers, manufacturers, distributors, and eventually consumers, increasing the price of stored goods.
Take this simplified case:
- Base cost of a product: $100
- 25% import tariff: +$25
- Additional logistics, warehousing, and handling (10%): +$12.50
- Retail margin markup (30%): +$40
- Final consumer price: ~$177.50
What began as a $100 product now costs almost 78% more. This increase is not due to its value, but to added costs.
Sectors relying on cross-border sourcing, including electronics, automotive parts, apparel, and consumer goods, experience particularly pronounced inflationary pressure. As businesses struggle to maintain margins, many have resorted to common mitigation strategies:
1. Sourcing Diversification
Companies are relocating manufacturing from tariff-heavy markets such as China to countries like Vietnam, India, or Mexico. This “China+1” or “Global+1” approach spreads risk and reduces overexposure to disruptions in a singular market.
2. Localizing Warehouses
Tariffs on finished goods can be avoided or delayed by importing components and assembling them locally. Additionally, distributing from domestic warehouses and being close to end markets reduces shipping costs and lead times.
3. Flexible Warehousing Models
Agile businesses now prioritize short-term, scalable warehouse solutions. This lets them quickly adjust to changing costs and demand. They avoid long-term leases and fixed facilities.
Operating with Greater Agility in an Inflationary Environment
In the current economic environment, managing costs requires more than just cost-cutting measures; it necessitates structural flexibility and adaptability. Traditional heavy-asset models with fixed infrastructure do not work well for brands. Brands need to respond quickly to policy changes or supply chain issues by choosing spaces offering real-time scalability.
Here are three critical capabilities for modern supply chain resilience:
1. Real-Time Scalability of Storage
Whether ramping up for peak season or downsizing during economic slowdowns, businesses need a storage solution that scales with demand, enabling quick adjustments. Static facilities can’t deliver this responsiveness.
2. Reducing Fixed Capital Pressure
Instead of spending a lot on permanent buildings, businesses are using on-demand warehousing. This changes fixed costs to variable ones. As a result, companies can free up cash for smart reinvestment.
3. Strategic Placement of Supply Nodes
By setting up several warehouses close to where customers are, companies can lower delivery costs. This also helps them handle disruptions and boost customer satisfaction. These are important goals in a market affected by inflation.
Cubework: A Space Solution in the Inflation Era
In the face of rising costs, Cubework offers more than just square feet—it delivers operational agility ideal for businesses navigating tariff-induced challenges.
We’ve built our nationwide network of flexible, commercial spaces for today’s fast-moving type of businesses. Whether you’re importing goods, managing seasonal inventory, or entering the U.S. market, Cubework provides the tools and locations needed to stay agile and cost-efficient.
Why Businesses Choose Cubework:
- Flexible lease terms – meeting short-term warehouse space needs—from weeks to months, without the burden of long-term commitments
- Move-in-ready warehouses – meeting temporary warehouse space needs—equipped for logistics, light manufacturing, and e-commerce fulfillment
- Strategic locations – near major ports, airports, and consumer hubs
- Integrated services – warehouse room, office space, showrooms, and loading dock access all under one roof
Seasonal Brand Reduces Costs by Localizing Inventory
A U.K.-based consumer electronics brand recently partnered with Cubework to optimize its U.S. operations. The company set up a short-term distribution center with office and warehouse space in Southern California. They did this to handle high shipping fees and port congestion during busy Q4 demand.
By moving inventory closer to their end customers, the brand:
- Reduced cross-border shipping by 22%
- Improved delivery time by 3–4 days
- Lowered warehousing overhead by 30% vs. traditional long-term leases
To support business growth and operational agility, the brand leased warehouse and office space through Cubework instead of committing to traditional real estate. It now uses Cubework seasonally, scaling up space during product launches and scaling down during low-volume periods. This flexible model has become central to its U.S. cost-control and real estate strategy.
Other Ideal Use Cases for Cubework:
- Importers/Brand Owners: Use U.S. warehouse space as a buffer between customs clearance and retail distribution.
- DTC/E-commerce Brands: Speed up last-mile delivery with forward-positioned inventory near major cities.
- Overseas Businesses: Test U.S. market entry with minimal infrastructure risk and full flexibility.
Conclusion: In Uncertainty, Agility Is the Real Edge
Tariff policy and inflation are two parts of the same economic issue. They both affect costs, pricing, and customer behavior. While some companies remain stuck reacting to change, others turn these challenges into competitive advantages.
Agility is the new operating model.
Businesses can use flexible infrastructure and local warehouses. They can also implement cost-effective logistics. This helps them create supply chains that adapt quickly and grow effectively. Cubework is proud to be part of that transformation—offering not just space, but a smarter way to manage it.
Regardless of whether you’re dealing with tariffs, inflation, or global expansion, we’re prepared whenever you are.
Preguntas frecuentes
1. How do tariffs contribute to inflation and higher consumer prices?
Tariffs increase the cost of imported goods, which are often passed along the supply chain as higher prices to consumers. This contributes to inflation by raising operational costs and, eventually, retail prices for consumers.
2. What strategies can businesses use to manage rising operational costs due to tariffs?
Companies can mitigate tariff-related costs by diversifying sourcing, localizing supply chains, leveraging flexible warehousing, and investing in data-driven inventory optimization.
3. How does Cubework help companies stay competitive amid inflation and tariff pressures?
Cubework offers nationwide, short-term industrial space solutions that enable businesses to scale operations, reduce fixed costs, and stay close to their end markets—improving agility and profitability.
Strengthen Your Cost Control Strategy
Cubework’s flexible warehousing network slashes 2025’s tariff costs and keeps your supply chain agile. Call 888-599-7809 or email info@cubework.com. Turn trade chaos into a competitive advantage.